- Home
- Solutions
- News and Events
- Hilti Blog
- The Digital Black Hole in our industry
The Digital Black Hole in our industry
For an industry that uses increasingly cutting-edge technology on their clients’ projects, construction companies still struggle to embrace tech that provides the same level of precision for the internal workings of their businesses. In fact, the McKinsey Global Institute’s Industry Digitisation Index rated construction as the second least digitised sector in the world.
With relatively few companies digitising their assets, business processes and working practices, a ‘digital black hole’ has formed in the construction industry. It’s a widespread problem that causes large projects to run approximately 20% longer than scheduled and up to 80% over budget. Construction companies are also spending an average of 90 hours each month searching for assets across jobsites.
Let's explore this topic in more detail...
Top costs for construction companies
Labour, materials and tools are the top 3 costs construction company’s have. They’re also the most difficult to manage – especially when using a patchwork of paper-based systems, sticky notes and spreadsheets.
This way of working is neither transparent nor accountable. It’s also easy for asset management to become dependent on specific individuals, making it difficult for anyone else to pick up the baton if a key person is out of the office. Such systems have negative cost and efficiency implications for managing physical and administrative assets too.
increase in prices
for all building work between December 2020-2021, due to construction material shortages [1]
of construction projects
are subject to delays [2]
of UK contractors
experienced labour shortages during the last quarter of 2021 [3]
of tradespeople
are unable to work as a result of tool theft, leaving them up to £3,000 out of pocket [4]
Labour costs
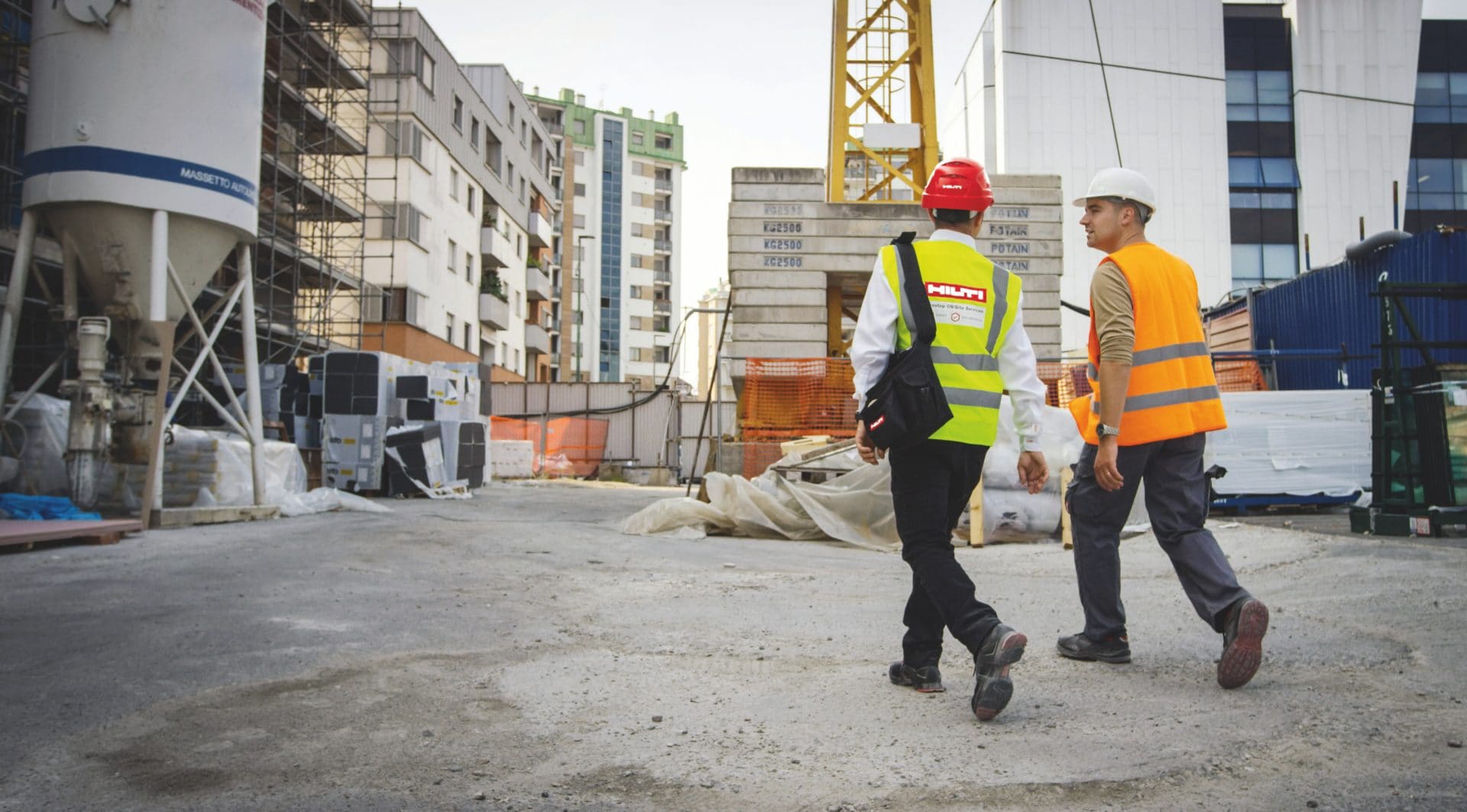
It’s no secret that labour costs and labour shortages in construction are on the rise. To combat this trend, businesses need to improve jobsite performance and become even more productive.
Labour efficiency is the basis of most tender estimates, as well as the yardstick by which performance is measured and monitored. However, labour efficiency is closely related to physical resources and ability in terms of knowledge and skills.
Advancements in technology are making management of labour productivity more predictable by exposing business inefficiencies. This can help improve planning and overall profitability.
To calculate labour productivity in your business, ask yourself these questions:
- How much work can a group of 20 workers get done in a day?
- If the number of workers is fixed, how many days do you need to complete the job?
- If the days you have to complete the job are fixed, how many workers will you need to finish on time?
- How much time can you save on finishing one part of the job if you invest in equipment that works faster?
Tool & equipment usage
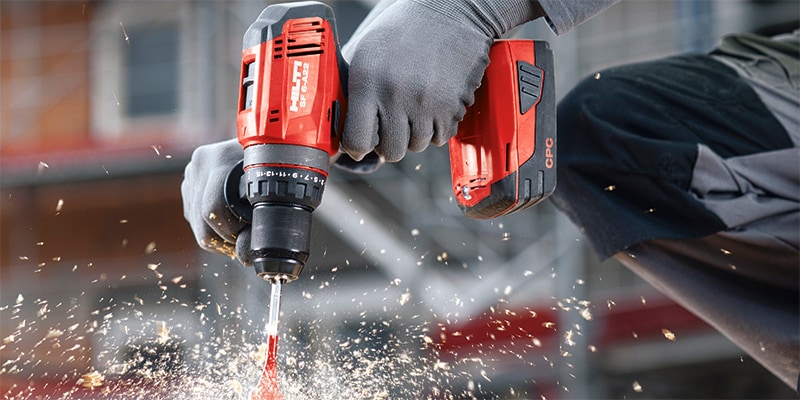
Mending the digital black hole in construction starts with prioritising digital technology, which creates a lot of data. Key data items can then be identified to enable quicker action for potential problems or applied to cultivate positive outcomes for future projects.
The construction industry’s digital adopters are harnessing IoT (Internet of Things) with the help of smart batteries to prevent issues like not knowing an asset’s location, usage information and maintenance status.
Smart batteries are equipped with built-in diagnostics that sync with a connected tool to relay information, providing a holistic view of the item including the battery performance levels, location and usage data. This provides key information to team members in real-time, which enables more informed tool crib decisions.
Material & Consumables Inventory Management
At a time when profit margins are getting tighter and cost of materials are rising, the use of paper-based inventory management systems that are dependant on people are impossible to justify.
Connecting smart batteries and tools to digital asset management software encourages predictability by monitoring inventory through a cloud-based platform. Since it efficiently tracks inventory and the usage of materials and consumables (such as nails, bolts and tool inserts), better estimates can be made when ordering. This can prevent duplicate assets and decreased productivity due to waiting around for the right materials.
Digital asset management software also helps prevent tools from going missing, by monitoring consumables usage and any unauthorised removal of equipment.
Final thoughts...
While the digital black hole may be common in the construction industry, digitising asset management is an opportunity to better control costs, reduce losses and keep projects running on time.
Digital solutions like smart batteries, connected tools and digital asset management software are increasingly easy to use and relatively inexpensive to implement. Construction technology will more than pay for itself very quickly – by cutting costs on physical assets, freeing up staff for more productive purposes and eliminating the delays caused by paper-based systems.
To learn more about how the digital black hole is impacting the construction industry and how Hilti can help your business, please fill out the form below and a member of our team will call you to discuss next steps!
Alternatively, you can register with us online and sign up to receive our newsletter - which contains exclusive updates on our latest technology and innovations.
(Already have an online account with us? You can manage your newsletter preferences here)
[1] Construction Materials Price Increases – What Can We Expect in 2022? - Glazing Vision
[2] Delays in Construction Projects: What We've Learnt | Cornerstone Projects
[3] Temporary visa's needed to tackle construction labour shortage (pbctoday.co.uk)
[4] Tradespeople left over £1000 out of pocket after tool theft (simplybusiness.co.uk)